3D Sculpting for 3D Printing
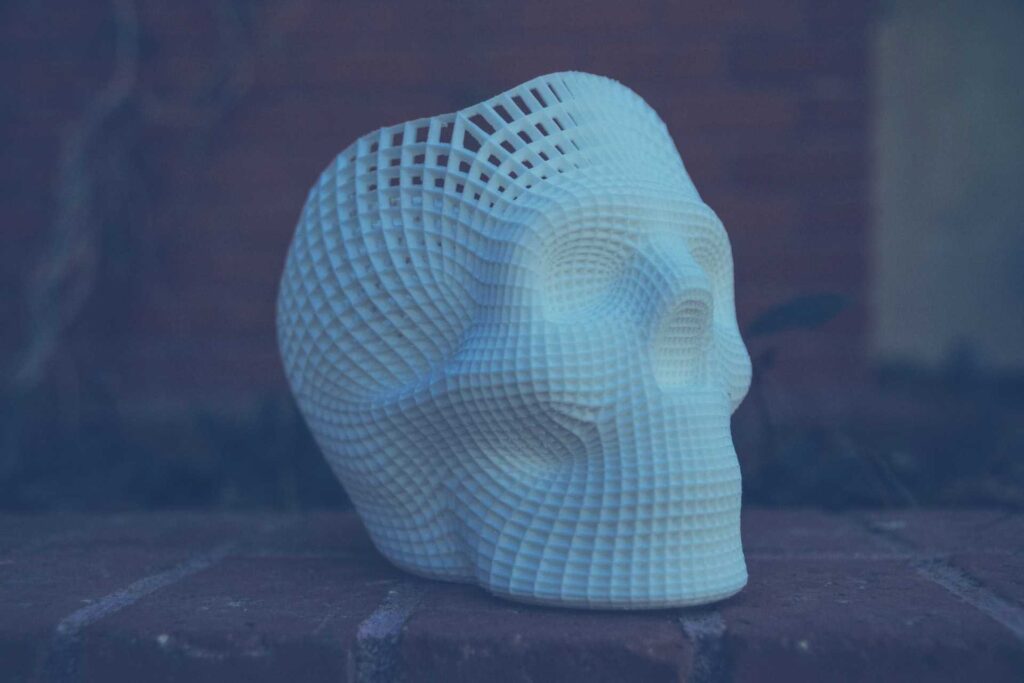
Printing on a 3D printer is a fairly simple process, if you follow the rules for working with different types of materials and with specific printer models, but with its own subtleties. To avoid unforeseen difficulties in the printing process, you should carefully study the 3D model before uploading the file to the 3D printer.
Three-dimensional modeling and printing of 3d models have found their application in many areas of human activity. They are in great demand today.
The creation of 3d models and the manufacture of a prototype of a finished product is now a necessary stage. It’s when starting the production of a new product. Also it’s when preparing a presentation to a customer. Or it’s when conducting functional testing of a new product.
3D modeling is essentially the creation
You can learn models for 3D printing in various programs designed to work with three-dimensional objects. The principle of object modeling in all programs is similar. But there are differences in the approach to solving problems. You can use professional applications for rendering 3D renders (The Brush, Autodesk Maya and 3ds Max and others). Can be used applications for engineers (Fusion 360, Autodesk Solidworks Blender, Compass 3D). There are also programs that are optimized for working with small 3D objects (Sketchup). The choice of software depends on the user’s habits since the usability of the program depends on the features of the interface.
Learning 3D programs in 3d sculpting services is not an easy task. So 3D modeling is a task for real professionals.
Novice users usually purchase entry-level FDM or SLA / LCD printers. FDM uses plastic filament for printing. In SLA and LCD, photopolymer printing technologies – liquid photopolymer resin. FDM printers are more affordable, and photopolymer printers allow you to create much more complex and detailed objects.
Creation of 3D characters
Of course, the most direct road to the video game industry is through specialized education. Nevertheless, many specialists working in this field have studied 3D modeling on their own or have taken short courses. Modern 3d modeling and sculpting is an interesting and complicated task.
Most photopolymer 3D printers recognize STL files.
You can create an STL file of a 3D model in a CAD program or using RangeVision 3D scanners, Einscan handheld 3D scanners, etc. STL and Gcode files should not be confused. STL files contain a 3D object, and a Gcode file is a slicer-compiled code to control a 3D printer. Many 3D printer manufacturers provide a test file in .gcode format so that the user can try out the new hardware right away. But what if you need to create a project for a 3D printer from scratch? Consider popular programs that make it possible to develop complex objects for different 3D printing methods.
Conclusion
Today 3D modeling finds many uses and 3d modeling and sculpting are everywhere. The process of modeling a 3D part for printing on a 3D printer. It is easy to master without taking lengthy expensive courses. In the modern information environment, there is a sufficient number of free and very informative, and easy-to-understand training videos. Reading thematic forums, participation in communities of 3D printers, where it is customary to help beginners and explain non-obvious and complex nuances, can also help.
3D modeling is a combination of mathematics, geometry and design. Files that are instructions for 3D printers can be created with special programs. The work of these programs is comparable to that of a sculptor, architect or builder – they demonstrate how an object will be created. If a drawing is a two-dimensional representation of a building, then a model is its three-dimensional layout, which provides a mathematical description of the object’s surfaces. In special programs, 3D designers create files that describe the position of points in space – in such models, many geometric shapes are involved. Ultimately, polygons and curves make up a 3D object.